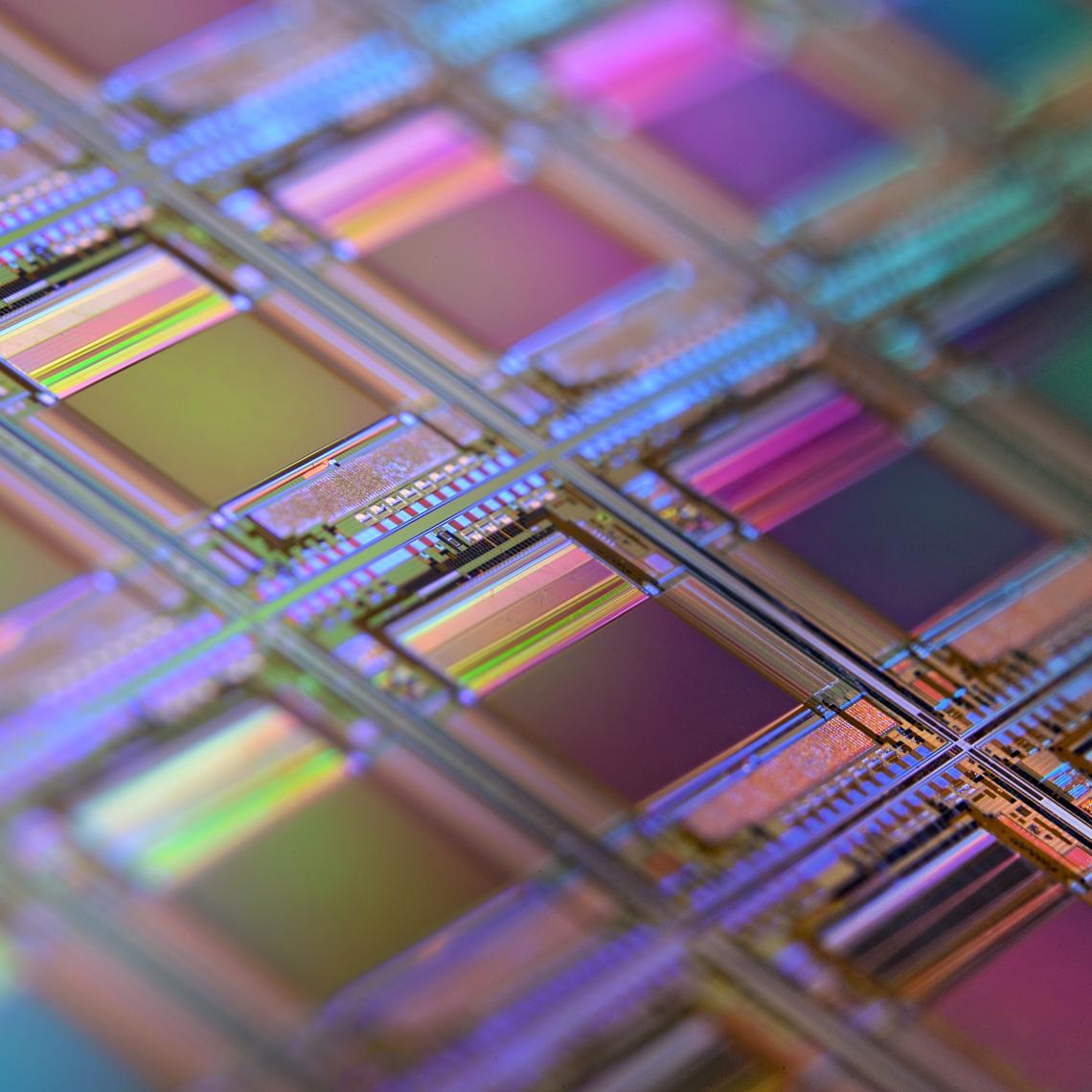
A macro of a silicon wafer. Each square is a chip with microscopic transistors and circuits. Image by Laura Ockel, available from Unsplash under CC license.
The Frontier of the Global Chip War: 1) the Delayed Justice?
Taiwan’s semiconductor industry has been under the global spotlight amid the chip shortage since 2020 and the rising geopolitical tech race among great powers. How have Taiwanese chipmakers silently become a central driver of the world economy over the past decades?
Quick Takes
- Before the current chip crisis, the prominence of the Taiwanese chip industry had long been overlooked.
- TSMC, the largest chipmaker in Taiwan, makes 92% of the most advanced chips used in smartphones or high-performance computers worldwide. By contrast, lower-tech chips for cars account for only 4% of its revenue.
- Founded in 1987, TSMC focuses on chip manufacturing. Since 2014, it has become Apple’s exclusive contract manufacturer for processors, making Apple one of TSMC’s best growth drivers.
- The Taiwanese government has played a crucial role in fostering the semiconductor industry. However, drought and power shortages pose challenges to sustainability in the sector.
Microchips are currently one of the most sought-after products in the world. Boasted as “the lifeblood of the modern economy”, they not only power electronic devices like computers and smartphones, but are increasingly indispensable for cars (more particularly electric vehicles) and appliances along with the rapid development of artificial intelligence (AI) and the Internet of Things (IoT).
Since 2020, the COVID-19 pandemic has driven up the consumption of mobile devices and PCs, as well as the adoption of cloud computing. PC sales rose by more than 50% in early 2021, while purchases of cloud data center chips increased by 30%. Coupled with the widespread supply chain disruptions brought by the pandemic, the exponential growth of the demand for chips led to a global shortage that lasts until today. The severe chip shortage has been particularly detrimental to the automotive industry, with all three major German automakers Volkswagen, Daimler, and BMW having to temporarily shut down their factories due to the lack of car chips. The new car sales in the EU fell by nearly 24% in 2020 and dropped to a record low since 1990 in 2021.
Even though most countries have gradually lifted COVID restrictions, company executives are still pessimistic about the chip supplies for the near future. In April 2022, Volkswagen CFO Arno Antlitz stated that he expected the structural undersupply of chips would continue until 2024.
As the supply of microchips becomes key to business growth and continuation across various industries, the semiconductor industry frequently stands at the center of the discussions about post-COVID economic recovery, which has repeatedly brought Taiwan to global attention over the past two years. Surprisingly, the self-ruled island accounts for 92% of the advanced chip production in the world, and Taiwan Semiconductor Manufacturing Company (TSMC), Taiwan’s largest chipmaker, holds the latest manufacturing technology in the industry.
Worldwide dependence on Taiwan for chip supply plays a crucial role. In early 2021 when the chip shortage was reaching its worst, US President Joe Biden’s top economic adviser, Brian Deese, and Germany’s then Economy Minister Peter Altmaier both sent an unusual letter to Taiwan’s Economic Affairs Minister Wang Mei-hua requesting help to resolve the shortfall.
Before the current “chip crisis”, the prominence of Taiwan’s semiconductor industry had long been overlooked. TSMC enjoyed way less fame on the global stage than its main competitors Intel and Samsung Electronics. How have Taiwanese chipmakers silently become a central driver of the world economy? This article looks back on the development of Taiwan’s semiconductor industry over the past decades to shed some light on its importance to the global economy and the challenges it faces today in the backdrop of the growing trend of deglobalization and the tech race among great powers.
With a current market capitalization of $492.96 Billion in June 2022, TSMC is worth much more than all the three German car giants (Volkswagen, Daimler, and BMW) combined.
The Overlooked Giant
If it were not for the “global chip war” brought by the pandemic, few people in Taiwan would have realized how valuable the island’s semiconductor industry is.
The semiconductor industry can be divided into three main business models: integrated device manufacturers (IDM), fabless, and foundries. IDM companies engage in designing, manufacturing, and sale of products; Intel and Samsung are the two most famous examples. Fabless Companies design and sell hardware while outsourcing the fabrication to a third-party manufacturer. The U.S. company Qualcomm is one of the world‘s leading fabless chip designers. The foundry model is created by Morris Chang, the founder of TSMC. Focusing solely on manufacturing, TSMC also promised its clients that it would never compete with them.
In an economy that strives to evolve from a manufacturing-based to a more innovation-oriented economic growth model, chip fabrication had long been deemed by the Taiwanese public as yet another industry that supplies goods to foreign brands and lacks cutting-edge technology. While many top players in the global industry, such as Intel and Samsung Electronics, are integrated device manufacturers (IDMs) that design and produce chips, most of the Taiwanese semiconductor companies – TSMC included – focus only on chip manufacturing and packaging.
Yet, by being a pure-play semiconductor foundry, TSMC was ranked as the world’s third largest semiconductor company by revenue since 2016, behind Intel and Samsung Electronics. Boosted by the growing chip demand, the company has experienced impressive growth since 2020: the first-quarter revenue rose 36 percent in 2022, with its stock price nearly doubling between 2020 and 2022.
“The value and importance of TSMC have long been underestimated. “It’s ‘delayed justice’ that its stock price reached more than $600 NTD [19 Euro] only now,” former TSMC spokesperson Elizabeth Sun stated in 2021.
With a current market capitalization of $492.96 Billion in June 2022, TSMC is worth much more than all the three German car giants (Volkswagen, Daimler, and BMW) combined. The importance of the Taiwanese semiconductor companies, TSMC in particular, lies not only in their market values but also in the technology they hold. According to a 2021 report by Boston Consulting Group and Semiconductor Industry Association, Taiwanese chips only take up 20% of the global production. But in the category of logic chips, which are the fundamental parts of computing that include microprocessors for mobile devices, PCs, AI systems, and supercomputers, as well as microcontrollers used in cars and industrial automation equipment, the contribution of the Taiwanese chipmakers is much more significant. More than half of the logic chips in the world are made in Taiwan, including 92% of the most advanced ones, which require chip process technology of fewer than 10 nanometers (ten-billionths of a meter).
The nanometer value of the chip process technology indicates the size of features, which are the smallest units manufactured inside the circuitry of a chip. Over the past two decades, the foundry process technology of logic chips has been evolving rapidly, with the size of features decreasing from slightly less than one micrometer (one-millionth of a meter) to five nanometers. The shrinking size of microscopic features enables more circuitry to be manufactured in the same space, preventing chip sizes from increasing as chips become more advanced. That is how PCs and mobile devices get lighter over the years despite their increase in performance. That is also why semiconductor manufacturing companies have been fiercely competing to lower the nanometer value of the chip fabrication process.
Only three companies in the world possess chip process technology of fewer than 10 nanometers: TSMC, Samsung Electronics, and Intel – with Intel launching its 10-nanometer technology only recently and a few years behind its competitors. This means that 92% of the Taiwanese market share in advanced logic chips is taken by TSMC alone, and most of the latest processors in the world rely on the supply from this single company. For example, the Apple M1 chip, released in 2021, is produced by TSMC’s five-nanometer technology – so far the most advanced chip process technology available for mass production.
Currently, TSMC and Samsung Electronics are racing to be the first to launch the 3-nanometer technology, with both plannings to start producing 3-nanometer chips in the second half of 2022. The two companies also share a roadmap for beginning 2-nanometer production in 2025. The Intel 3-nanometer process is to enter mass production only in 2023.
TSMC’s Tech Empire
Among the leading semiconductor companies globally, TSMC is a rather latecomer. Founded only in 1987 (in contrast to Intel in 1968 and Samsung Electronics in 1969), the company silently rose from one rented “fab” (a common term to call a semiconductor fabrication plant) to a global star dominating the supply of one of the most significant products for the world economy. Meanwhile, its chip process technology quickly caught up by evolving from three-micrometer in 1987 to three-nanometer in 2022.
Many attribute TSMC’s success to its “pure-foundry” model, a rather unique and innovative business setup in the semiconductor industry worldwide at the time when TSMC was founded. TSMC’s founder Morris Chang recalled that most of the world’s semiconductor companies have chosen to implement the IDM model that integrates chip design, foundry, and marketing. But in the 1980s, Taiwan did not have the design and marketing capacities to establish a vertically integrated company. Chang then decided to have TSMC focus solely on chip foundry. To gain trust in the highly competitive and technology-intensive semiconductor industry, he also promised that TSMC would never compete with its clients or produce self-designed chips.
Although TSMC’s business model was tailor-made for Taiwan back then, Chang’s decision about the onset of globalization stays a good call until today. TSMC keeps winning over the world’s leading fabless semiconductor companies, which design microchips but do not own their manufacturing plants, such as Apple, AMD, ARM, Broadcom, and Nvidia. At the same time, by focusing on foundry, TSMC has been able to concentrate its resources on improving its manufacturing process.
According to Chang, although Taiwanese semiconductor technology was falling behind at the time, “the wafer yield was so good that it could compete with other world-class companies”. A wafer is a thin slice of a semiconductor like silicon that microchips are produced from, and wafer yield means the percentage of microchips in a finished wafer that pass all tests and can be sold.
Between 1990 and 2010, TSMC went through steady growth and a series of expansions, establishing more than ten new factories, including one in Washington State, the US, and one in Shanghai, China. In 2001, the company launched its first mega-fab, an innovative setup of several fabs coordinated by a centralized fab manufacturing management system, in Hsinchu, Taiwan. The mega-fab remains to be TSMC’s global headquarter until today and is also its first 12-inch wafer factory. “12 inch” refers to the diameter of the silicon wafers used for production. Using larger wafers means more chips can be produced from a single wafer, lowering the unit cost of manufacturing a single chip while simultaneously adopting more modern production requirements. Today, the most modern chip manufacturing process is still based on 12-inch wafers, while 8-inch wafers are used to produce older chips.
The year 2010 marked a significant turning point in TSMC’s development history. Having gone through the 2008 financial crisis, the company boldly doubled its capital expenditures from $2.67 billion to $5.93 billion to accelerate the launch of the 28-nanometer process technology, which was in high demand then. The following year, TSMC’s 28-nanometer process began mass production, increasing its advantage over its competitors like Samsung Electronics and GlobalFoundries. In 2012, Chang claimed that TSMC’s 28-nanometer process was “a roaring success”, taking nearly 100% of the global foundry market share.
Following the success of its 28-nanometer process technology, TSMC leveraged its technology advantage to ride the wave of smartphones. In 2014, the company took Apple’s processor foundry order for the first time to produce the A8 processor for iPhone 6 with the 20-nanometer process technology. Before that, Apple relied solely on Samsung Electronics to manufacture its smartphone processors. For the A9 processor for the iPhone 6s, TSMC and Samsung Electronics both won the order; however, TSMC used its 16-nanometer process to beat the latter’s 14-nanometer technology by quickly upgrading its chips for higher performance. Some experts said that Samsung Electronics’ 14-nanometer technology was not mature enough at that time, because it jumped directly from 28-nanometer to 14-nanometer, instead of gradually evolving from 28-nanometer to 20-nanometer, and then 16-nanometer like TSMC.
Since then, TSMC has replaced Samsung Electronics as Apple’s exclusive contract manufacturer for processors, making Apple one of TSMC’s biggest growth drivers in recent years. In 2021, 44% of TSMC’s net revenue came from smartphone chips, while automotive chips, which Altmaier requested TSMC to produce for German automakers, only accounted for 4%.
TSMC’s development illustrates how the technology competition among chipmakers is primarily a capital race. To remain competitive in advanced chip manufacturing processes, steady and heavy investments in R&D and equipment are a prerequisite. Only TSMC, Samsung Electronics, and Intel are now left with powerful capital to compete.
For example, when a chipmaker wants to move to more advanced process technologies below the 7-nanometer, it must use extreme ultraviolet (EUV) lithography machines from the Dutch equipment manufacturer ASML. These machines, which cost more than $100 million each, are one of the factors driving up the capital expenditure of TSMC and its competitors. In 2018, GlobalFoundries, once among the forerunners in chip manufacturing technology, announced that it was stopping the development of 7-nanometer chips due to the high cost.
TSMC seems to continue staying fierce in this capital race. In October 2019, the company increased its capital expenditures on its 7-nanometer and 5-nanometer technology, which was first launched in 2019 and is currently still in the process of product upgrades. In April 2021, TSMC announced that it would invest around $100 billion through the next three years to increase its production capacity by building 12 new fabs to support the manufacturing and R&D of leading-edge and specialty technologies.
Science Parks: Cradle of the Taiwanese Semiconductor Industry
Besides TSMC’s contribution as an industry leader, support from the Taiwanese government also plays a crucial role in the rapid development of Taiwan’s semiconductor industry. 48.3% of the initial funds for the foundation of TSMC came from the Taiwanese government, and the company’s first fab was rented from the government-backed Industrial Technology Research Institute (ITRI).
The US White House’s 100-Day Reviews report on supply chain resiliency also highlights the Taiwanese government’s deep involvement in its semiconductor industry. It cites the analysis from the US Department of Commerce that Taiwan’s subsidies for chip fabrication facilities include 50% for land costs, 45% for construction and facilities, and 25% for semiconductors, in addition to R&D investments and other incentives. In contrast, South Korea and Singapore offer subsidies to reduce 25-30% of the cost of semiconductor facility ownership.
The Taiwanese subsidy model applied to its semiconductor industry derives from the concept of export processing zones (EPZs). In 1966, the Taiwanese government established the first EPZ on the island to attract foreign investments by giving tariff exemptions on imported raw materials and components used to produce end products for export in the EPZ. The EPZ policy drove Taiwan’s unprecedented economic growth, with its GNP up by 360% between 1865 and 1986, boasted by some observers as the “Taiwan Miracle”.
However, in the late 1970s, the EPZ growth model was hit heavily by the 1973 oil crisis, the 1979 energy crisis, and the 1970s recession in North America and Europe, which forced the Taiwanese government to look for alternatives and transform Taiwan’s economic structure. At the same time, many Taiwanese electronic companies had evolved from assemblers to manufacturers that directly produce electronic components in Taiwan to reduce transport costs, which formed a solid foundation for developing the tech industry. As a result, in 1975, the Taiwanese government mapped out a plan to establish science parks in Taiwan and created the Applied Technology Research and Development Group to execute the plan.
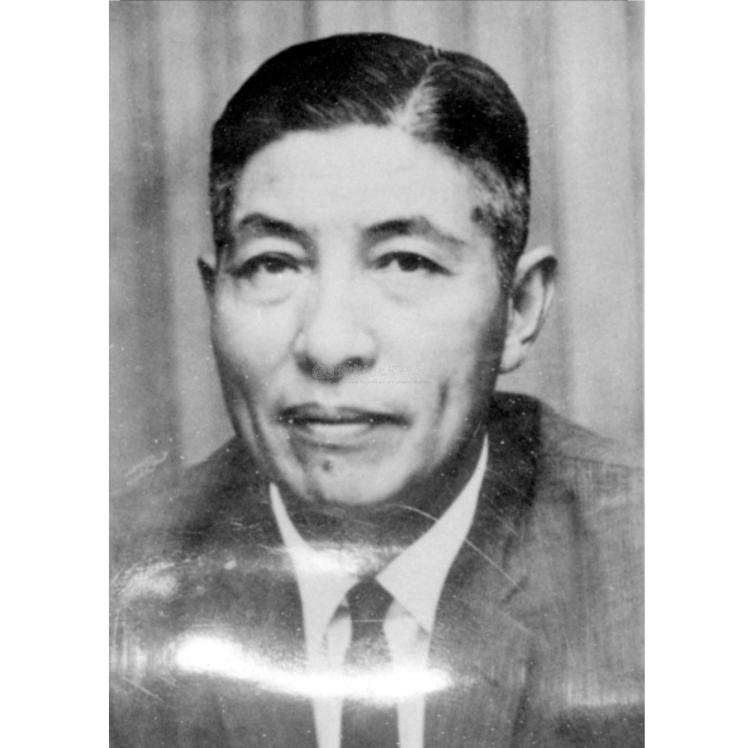
Kwoh-Ting Li (1910 – 2001) was viewed as the "Father of Taiwan's Economic Miracle" and the "Godfather of Technology" in Taiwan. Image by CNA available at Wikimedia Commons under CC license.
The group was led by the economist and politician Kwoh-Ting Li, also the designer of Taiwan’s EPZ policy. In 1977, Li went on a study trip to Silicon Valley and Stanford University in the US. After he returned to Taiwan, he proposed to build a similar tech industry development model that brings businesses and research institutes together in Hsinchu, a city in northern Taiwan where two of Taiwan’s top universities and the ITRI are situated.
The Hsinchu Science Park was founded in 1980. Unlike most science parks in other countries, the Hsinchu Science Park operated more like an EPZ in its early years. For example, the Taiwanese government held full land ownership to prevent companies from reselling land for profits. Businesses in the science park also enjoyed tax exemptions and were mainly export-oriented.
At the same time, as the Taiwanese government expected the Hsinchu Science Park to lead the industrial upgrading in Taiwan, the Taiwanese science park had some innovative aspects compared to its EPZs. For instance, companies in the science park were required to contribute a certain portion of their revenues to R&D. Besides, to attract the Taiwanese tech professionals who had studied and worked in the US, the Taiwanese government also founded a bilingual school and built Californian-style mansions and residential areas in the Hsinchu Science Park.
With substantial support from the government, the Hsinchu Science Park has achieved significant results and witnessed the birth and growth of Taiwan’s top semiconductor companies like TSMC, United Microelectronics Corporation (UMC), Powerchip, and Vanguard International Semiconductor Corporation (VIS).
Based on the success of the Hsinchu Science Park, the Taiwanese government has continued to set up more science parks in other parts of Taiwan to further boost its technology industry and maintain regional development. Taiwan’s second science park was founded in Tainan, a city in southern Taiwan, in 1995. Researcher Jou Sue-ching notes in her paper published in 1998 that the establishment of the Tainan Science Park was an important milestone in the development of Taiwan’s tech industry. The Taiwanese government gave more power to private companies to decide how to operate their businesses and promote the industry. As Taiwan’s tech industry was more advanced at the time relative to the 1980s, companies were less dependent on government funds and created more diverse funding models. However, industry giants like TSMC and UMC were consulted by the government before establishing the Tainan Science Park to ensure their intention to build new plants in southern Taiwan.
Currently, 12 science parks are spreading across western Taiwan, and many Taiwanese tech companies have their plants set up in multiple science parks. TSMC, for example, owns fabs in the science parks in Hsinchu, Tainan, and Taichung, a city in central Taiwan. According to Sun, operating manufacturing plants in different parts of Taiwan reduces the risk of being affected by earthquakes, which are frequent in Taiwan. At the same time, the three science parks are only around 100 kilometers away from each other, which simplifies staff deployment between fabs. TSMC founder Morris Chang mentioned that with the Taiwan High-Speed Rail launched in 2007, TSMC engineers in Hsinchu, Tainan, and Taichung can go back and forth in a day to provide frequent cross-fab support.
The prosperity of Taiwan’s tech industry, especially the boom of its semiconductor sector over the past two years, has also driven the development of the surrounding areas of the science parks in Taiwan. Sinshih District, where the Tainan Science Park is located, had been a rural area full of rice fields. Since TSMC announced the expansion plan of its fabs in the Tainan Science Park in 2020, the local real estate market has gone through exponential growth, with new residential buildings popping up one after another on former agricultural land. TSMC expects to put the most advanced 3-nanometer chips in mass production in its new Tainan fab in the second half of 2022.
Chip Shortage: A Sweet Trouble
Contrary to the widespread concerns in Europe and the US, the current global chip shortage has brought opposite sentiments in Taiwan. Many people are thrilled by the island’s economic growth led by Taiwanese chipmakers, and by the significant role of Taiwan’s tech industry on the global stage, dubbing TSMC “the sacred mountain that protects the country (護國神山)”. In 2020, when the global GDP growth rate plummeted to -3.5% due to the pandemic, Taiwan’s GDP rose by 3.11%. Its GDP growth further reached 6.28%, a record high in the past 11 years, in 2021. During a speech addressed to the top members of her party in February 2021, Taiwan President Tsai Ing-wen said that Taiwan now had “an unprecedented opportunity” to grow its economy, as talent and investments continue to move into Taiwan.
At the same time, the worldwide reliance on Taiwanese chipmakers is expected to give more leverage in international relations and national security to Taiwan, which has been struggling to counter China’s blockade in the international area and threat of invasion. When the Taiwanese government encountered difficulties purchasing COVID-19 vaccines in early 2021, TSMC CEO Wei Che-chia asked US Commerce Secretary Gina Raimondo for help getting access to the vaccines during an exchange related to chip supply. Weeks later, the US delivered 2.5 million COVID-19 vaccine doses to Taiwan, more than tripling the amount that Washington previously planned to allocate. In a paper published in November 2021, US scholar Jared McKinney suggests Taiwan should adopt a “broken nest” strategy to protect itself, threatening to destroy chip manufacturing facilities and “immobilize” its tech industry if Beijing invades.
However, the advantages do not come without burden. While companies and governments continue to pressure Taiwanese chipmakers to increase production, especially for auto chips, the global chip crisis is still far from the end after two years. Jackson Hu, former chairman and CEO of UMC, pointed out during an interview with Initium Media that the current chip shortage happened because many automakers fell behind tech companies to place orders while the growing development of 5G drove up the chip demand. Some tech companies even overbooked to ensure sufficient supply. For example, in late 2019,when the Trump sanction against Huawei, China’s 5G gaint, was underway, TSMC reportedly began ramping up the output of Huawei’s 7-nanometer chips. According to Bloomberg, “the Taiwanese contract manufacturer eventually shipped more than 2 million units at Huawei’s behest ahead of the sanctions cutoff”.
Although many have called on Taiwanese chip producers, particularly TSMC, to relieve the current shortage of automotive chips, Taiwan is not the main global supplier in this chip category. The global market of automotive microcontrollers, which are the most demanded car chips at the moment, is dominated by European IDMs like NXP, Infineon, and STMicroelectronics. According to an analysis released in May 2021 by the Institute for Information Industry, only 15% of these IDMs’ auto chips are outsourced for production, among which TSMC accounts for 60-70%. Facing the growing demand from automakers since late 2020, auto chip IDMs have turned to chip foundry companies for help to drive up production. Wu Chin-jung, general manager at Explore Microelectronics, a Taiwanese chip designer, told Business Next Media that the change in the number of orders was reflected by TSMC’s quarterly fiscal reports, which show its revenue growth from automotive chips turning positive in the fourth quarter of 2020, following the two previous quarters’ negative numbers.
Despite the seemingly attractive business opportunity, it is not easy for chip manufacturers to ramp up production in a short time. The most urgently-needed automotive chips are mostly produced from 8-inch wafers, instead of the most advanced 12-inch wafers, and the 40 8-inch wafer fabs in the world (15 in Taiwan) have all reached their full production capacity. Fang Leuh, chairman and president of VIS, which is one of Taiwan’s top chipmakers dedicated to chip production from 8-inch wafers, explained during a press conference in early 2021 that building new 8-inch wafer fabs is not only a question of funds, but it is a long-term investment that might receive low returns when the demand falls in the future, and many equipment suppliers have already stopped producing certain machines required for 8-inch wafers.
Accelerating the manufacturing process is also not an ideal solution. Most chipmakers withhold from adopting the “Super Hot Run” method, which can cut production cycle times by up to half, to produce automotive chips. Although it can shorten the manufacturing time to 20-25 days, the performance of the production equipment would be reduced, and the profit rate would be lower due to the increased costs. After receiving heavy pressure from all over the world, in May 2021, TSMC agreed to increase its output of auto chips by 60% for the rest of the year, reportedly by bringing in the “Super Hot Run” practice.
Environmental Challenges
Moreover, the Taiwanese chip manufacturers are facing growing disruption risks brought by drought and power shortage. In early 2021, western Taiwan experienced the most severe drought since 1947, which forced science parks across Taiwan to cut down water usage by 15%, with some factories relying on tank trucks to supply water. Although the water shortage was resolved in mid-2021, some worry that water supply might be under pressure again in dry years, as TSMC, which currently accounts for one-third of water consumption of the science parks in Hsinchu, Tainan, and Taichung, will almost double its water demand after its new fabs start operating.
On the other hand, power supply remains a pressing issue for the Taiwanese government. Taiwan’s electricity grid is old, and its power generation capacity is expected to decrease between 2021 and 2024 because its main power distributor Taiwan Power Company plans to retire several nuclear and coal-fired power plants during this period as a part of its energy transition effort. Concerns about electricity shortage in Taiwan have deepened after three massive power outages occurred in May 2021 and March 2022, with the latest affecting five million households and causing short “power dips” in several TSMC plants. Taiwan’s Ministry of Economic Affairs estimated that Taiwan’s power consumption would increase by more than 10% between 2018 and 2025 due to the growing demand from the tech sector, notably the energy-intensive semiconductor industry. Currently, TSMC alone takes up 5% of the national electricity usage.
The Changing Landscape
The current chip crisis has not only brought Taiwan to the world’s attention but also raised the priority of the semiconductor industry on many governments’ agendas. For Taiwanese chip foundry companies, a greater challenge ahead is the fiercer international competition triggered by the shift of attitude towards globalization, particularly in the US and the EU, and the ongoing tech race among great powers. While China has been striving to reach chip self-sufficiency for several years, the US and the EU have recently laid out their plans to localize chip production in the next few years.
This has made the Taiwanese government and chipmakers realize that the “global chip war” is not merely about reliving the current chip shortage, but rather a long-term battle for technology sovereignty. It has become increasingly clear that being at the frontier of this battle, Taiwan needs to take more action if it wants to guard its dominance in the semiconductor industry. The upcoming article will look at the latest developments of the “chip race” and how Taiwan responds to the growing competition from other countries.